Robotics Competition
Oct 2021 - Dec 2021
During my third year of college, I had the opportunity to participate in an exciting robot competition as part of a three-member engineering team. With only seven weeks to conceptualize, design, fabricate, and test our robot before the competition day, we faced a tight timeline. Despite competing against 40 other teams, many of which had four team members to our three, our innovative, reliable, and efficient robot design propelled us to a first-place victory without a single loss.
To qualify for the competition, our robot had to adhere to several design restrictions. It had to fit within a 10”x10”x10” cube and be constructed exclusively using a set of pre-provided materials, including limited sheet metal, acrylic, aluminum rods, and DC motors. We were limited to utilizing four electrical inputs, each with three positions: forward, neutral, and reverse. Additionally, the total 3D printed volume could not exceed 50 cubic inches, and individual prints had to fit within a 4”x4”x4” cube. Detailed contest rules and scoring guidelines can be found here.
Considering these design restrictions and the objective of our robot—picking up, carrying, and delivering small boxes from challenging locations in the arena to the center platform—we began a meticulous design process. After deliberating on nine possible design paths using a comprehensive Pugh chart, our team unanimously settled on a forklift-inspired design.
The chosen design featured a two-wheel drivetrain, a four-bar linkage lift arm, and a 180+ degree rotatable actuating fork. This configuration allowed our robot to reach the most difficult-to-access boxes in the arena while maintaining simplicity and reliability. Dividing responsibilities, each team member took the lead on designing and fabricating one section of the robot. In my case, I took charge of the critical intake mechanism—the actuating fork—which played a pivotal role in interacting with the boxes.
My design process began with initial rough hand sketches and force/torque/power/energy analysis, which I documented and can be observed below:
After confirming that our available geared motor provided more than sufficient torque and power to carry two boxes simultaneously, I proceeded to create the first CAD model draft of the design. Attached below is an annotated figure of the CAD model that I used to communicate this design to my team members:
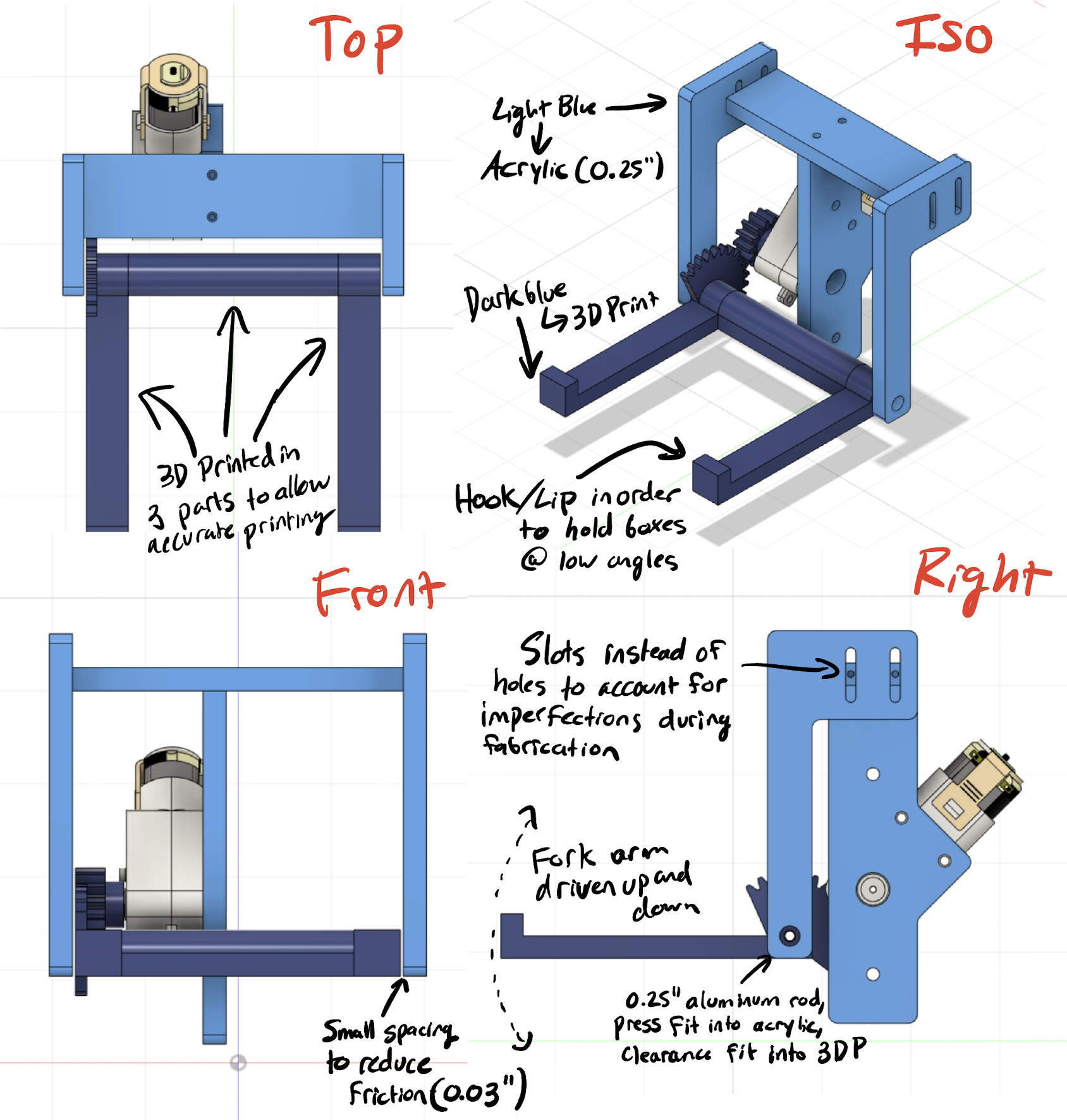
After modeling this design with CAD software, I quickly fabricated an initial prototype using a combination of 3D printing, laser cutting, manual milling, hand tools, and a bandsaw. This first iteration demonstrated the assembly's ability to successfully pick up two boxes and deliver them elsewhere, as pictured in the following proof-of-concept video:
However, during the testing phase, I noticed slight flexing in the acrylic components over the span of a week, likely due to the fact that forces were applied at the bottom while the only contact points were located at the top. Recognizing the potential for future complications, I promptly iterated on my design by reinforcing the assembly's bottom with an aluminum rod. This modification, illustrated below, also featured minor adjustments to the fork and gear dimensions. Ultimately, this became the final design of the fork assembly, which proved to be flawlessly functioning, consistent, and efficient.
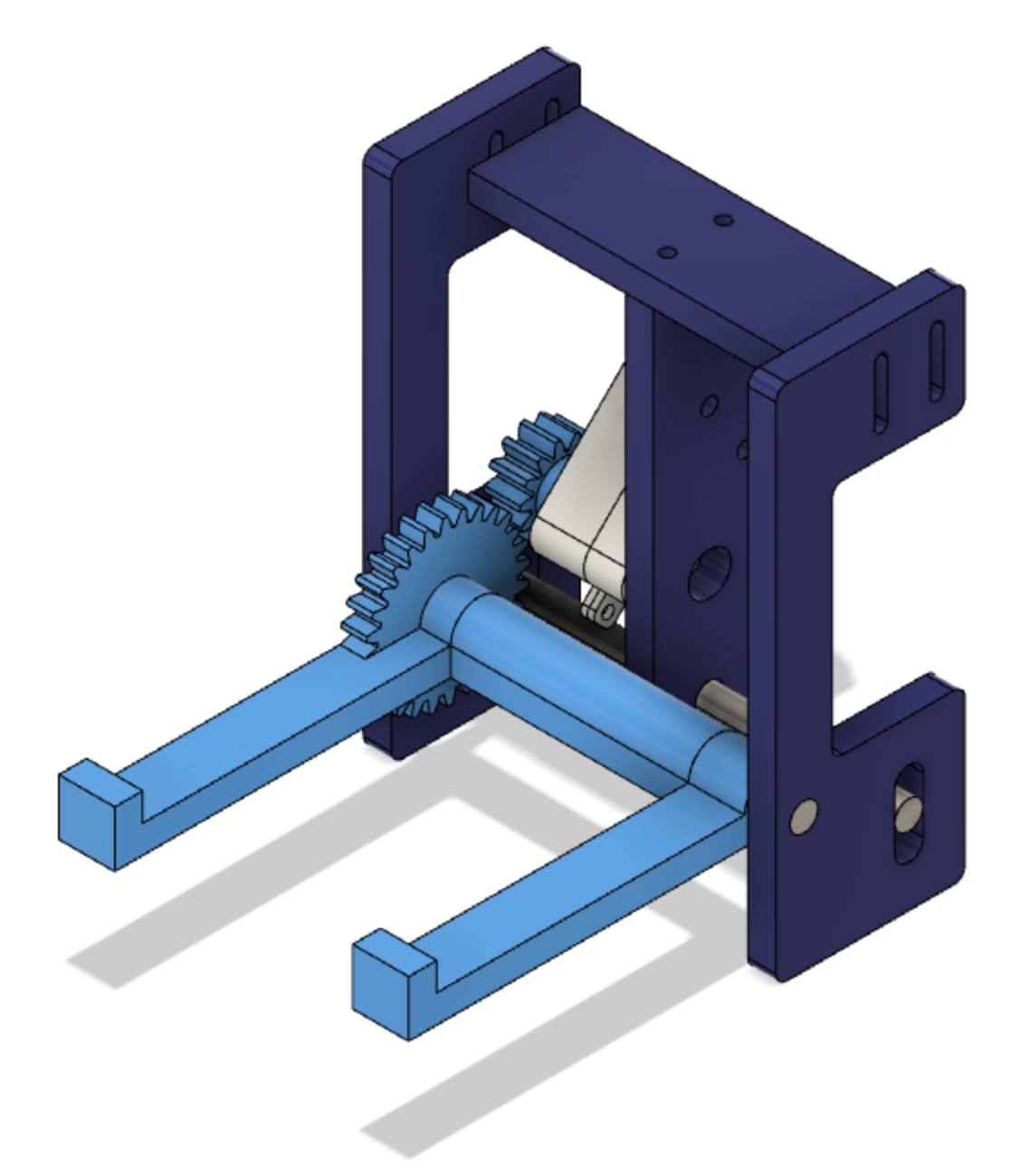
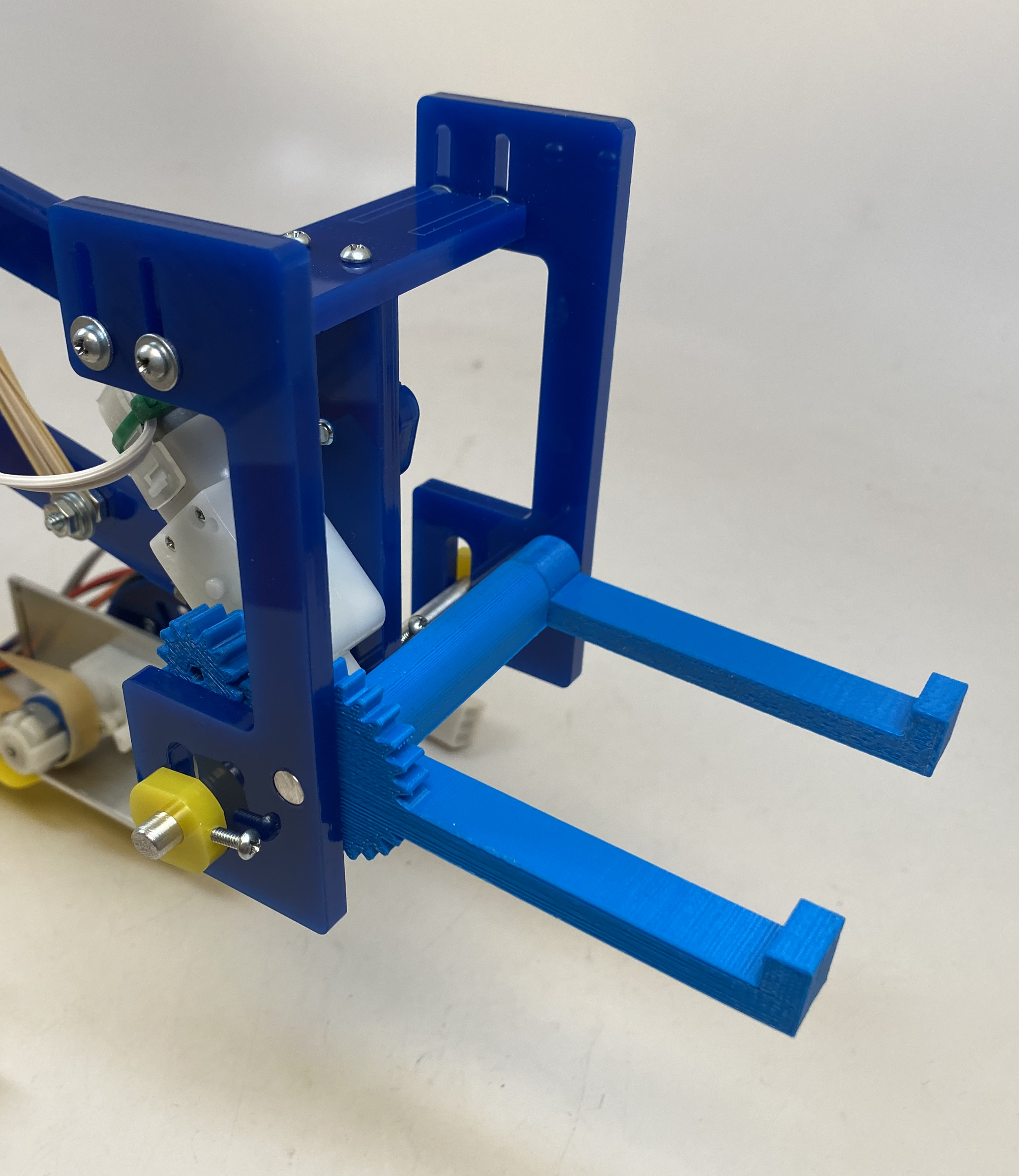
As each team member completed their final design and fabrication processes, we assembled all the components to create the fully functional robot. The CAD model of the assembly, as well as the realized product, are both depicted side by side below:
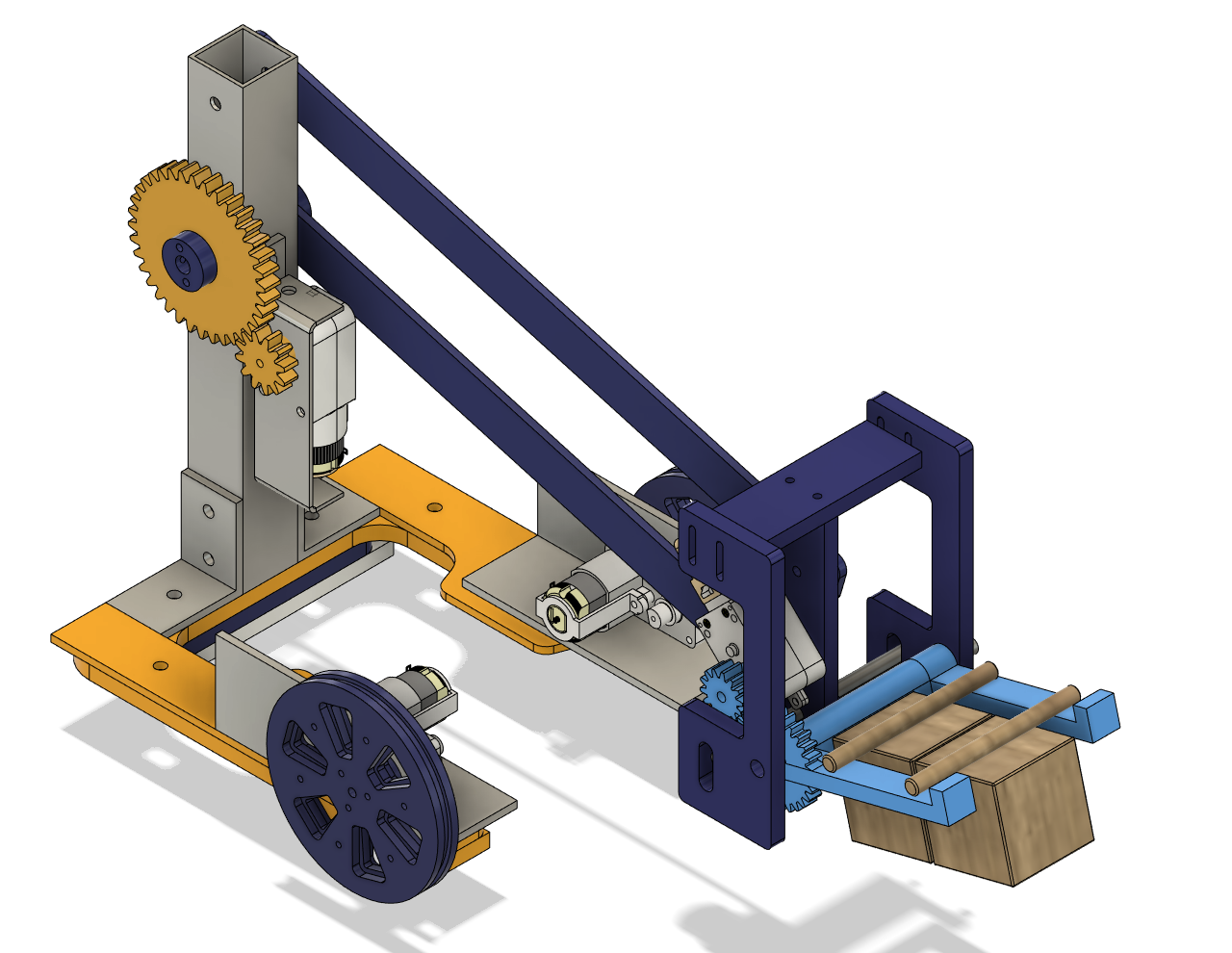
The last step involved extensive test runs in the practice arena. Once we mastered the robot's controls, our team achieved a perfect record during a test run, maximizing point values and multipliers by strategically placing boxes of various difficulty. We documented this test run, including timing, as seen in the following video:
On the highly anticipated competition day, our team was thoroughly prepared and confident in our robot's performance. Two of my teammates operated the robot, with one controlling the lift arm and fork, and the other managing the two wheels. While my teammates focused on the controls, I assumed the role of monitoring our scored points and time remaining, observing our competing team, and making critical split-second decisions for our team. The tournament began with three separate brackets, each of which were single-elimination, which allowed no room for error. Demonstrating remarkable consistency, we emerged victorious in every round, winning our bracket and securing our position as one of the top three teams.
Advancing to the top 3 bracket, we faced double-elimination matches where losing teams had one chance to make a comeback. However, our team's win streak continued, and we emerged victorious in each round, without needing to utilize our possible loss. In the end, we earned a first place victory in the highly competitive competition featuring 41 teams. This exciting experience highlighted our ability to work collaboratively, adapt to challenging constraints, and deliver a well-engineered final product under tight deadlines.
If you have any questions for me about our design process, additional documentaion, or anything else, please feel to contact me here. Thanks for reading!