Aerospace Mechanical Engineer at TRL11
Aug 2023 - Present
Statements expressed here are solely my own and do not represent the views or opinions of TRL11.
This chapter of my professional career is still ongoing, and I'll never be able to compress the incredible amount of experience and knowledge this job has afforded to me into this one webpage alone. And while I can't delve into the specifics of the design and fabrication process of our products, I can give a quick summary of what is already available to learn about us at TRL11.com, and my involvement in it.
In short,
We create space-rated video systems at TRL11. History has shown that high quality, low latency video in space proves to be very difficult, which is why almost any video you see from space is either high latency (not live, but recorded), or pretty low quality. We aim to change that, by using novel compression techniques powered by AI, tailored to the environment of space. That's what our software team is for.
As for myself, I'm the primary mechanical designer for a few of our product lines. From cradle to grave, I get to manage the physical design of these products, which also means making sure that these video systems survive testing, integration, launch, and operation for the full lifespan of the mission. This involves countless considerations, including (but definitely not limited to) structural integrity, thermal performance, dampening of vibrational modes, discharge of static buildup, electromagnetic compatibility, and protection from the harsh radiation of the sun. Every single one of these considerations must be adequately designed for and validated. In fulfulling these needs, I've had the opportunity to hone wide array of technical skills, which I've laid out at length at the bottom of this page.
First Projects
I kicked off my employment at TRL11 by assisting in a product that was already in the design process - the Triclops camera system, our three-camera assembly well suited for any RPO application. Whether it was wrapping up the design work, ensuring perfect manufacturability, creating and executing validation plans, or creating marketing materials, there was always plenty of work to be done for Triclops.
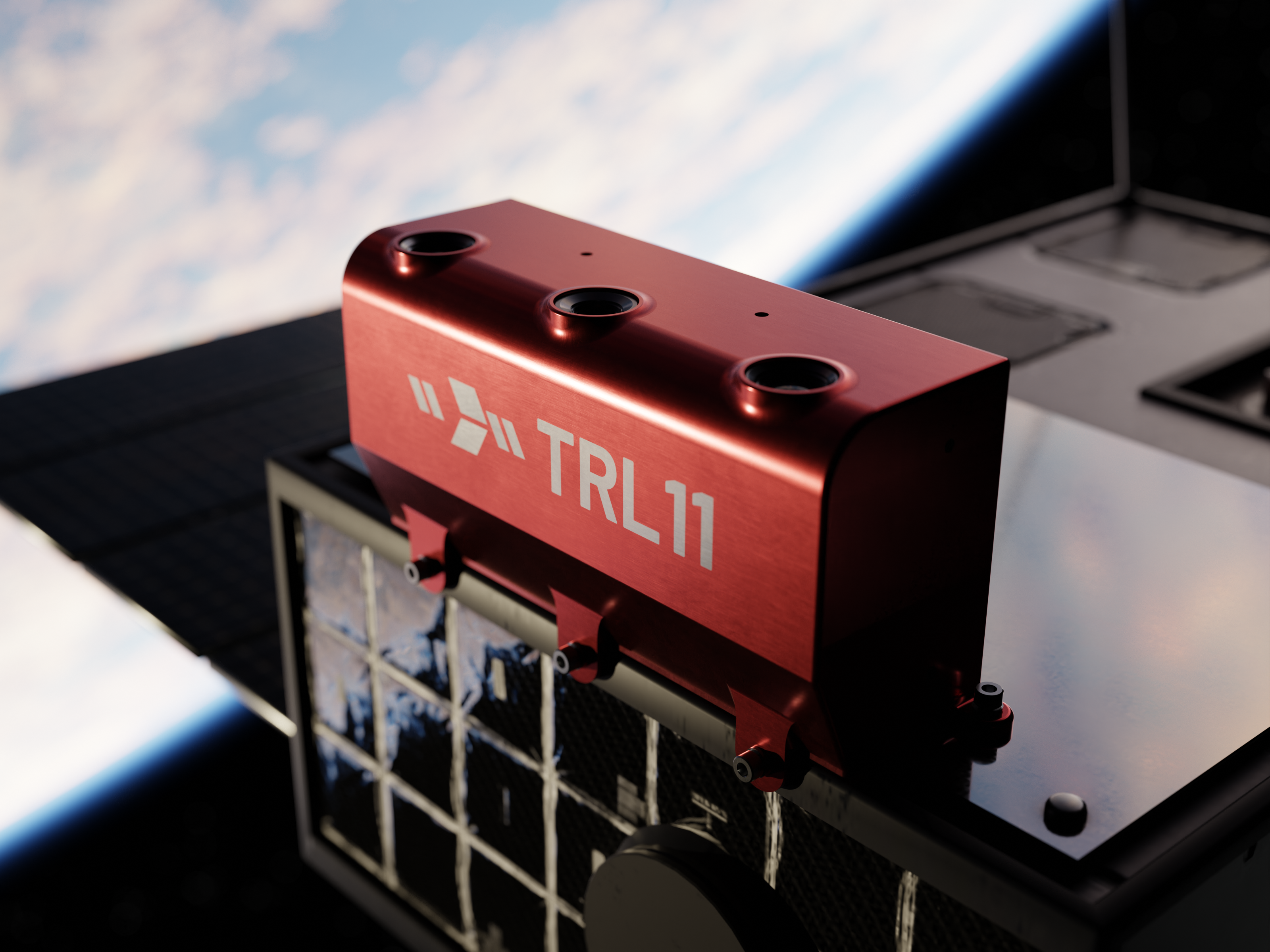
The above render and all others on this page were created by me in a 3D rendering software separate from our CAD software. Our current rendering pipeline just wasn't giving us the dynamic, photorealistic images we needed, so one of my early contributions to TRL11 was suggesting to move our rendering process to a software more suited for the job. I hadn't had any experience with it at the time, but as the saying goes, you get to wear many hats (and in turn, learn many new skills!) at a startup. Now, I can confidently produce high quality renders of new products on short notice.
Product Design Ownership
As we wrapped up the design of Triclops for one of our clients, we began to branch out and refine other product lines, as well as to develop entirely new ones.
SAVER
SAVER, our smart, space-ready DVR, already had flight heritage on previous missions, but after feedback from clients regarding desired features and interfaces, a full-scale redesign was in order. This was the first project that I assumed ownership of, from the first conceptual diagrams all the way to the flight-ready hardware getting strapped to a rocket.
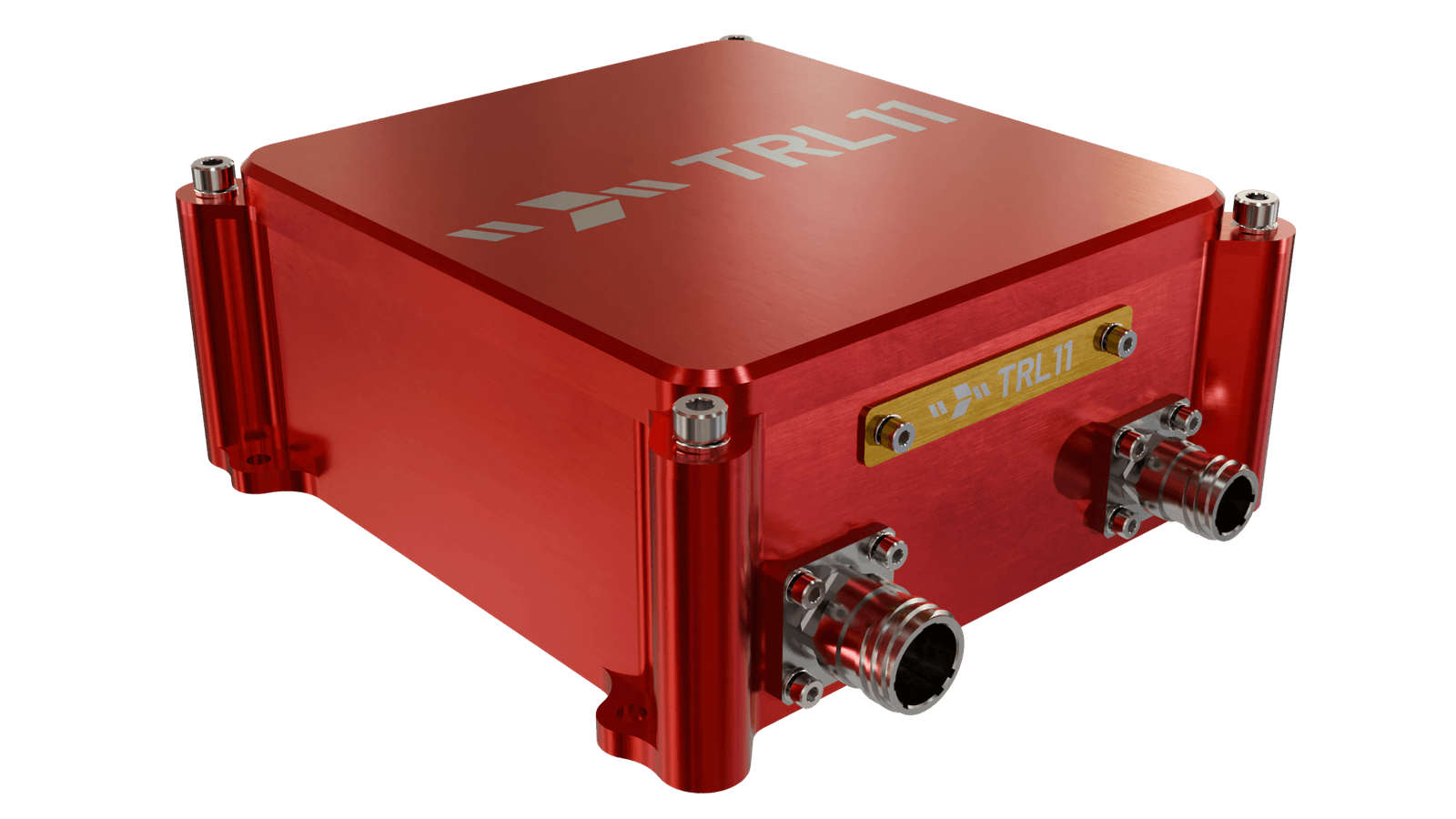
Fovea
Along with a SAVER redesign, we decided to design a line of standalone camera systems - Fovea. I was responsible for one of the products of this line - Fovea-M2. Fovea-M2 is our ultra-compact version of Fovea, trading optical fidelity (1080p instead of 4K) for a smaller footprint and mass. Like SAVER, I assumed ownership of Fovea-M2 from design conception to flight-ready cameras.
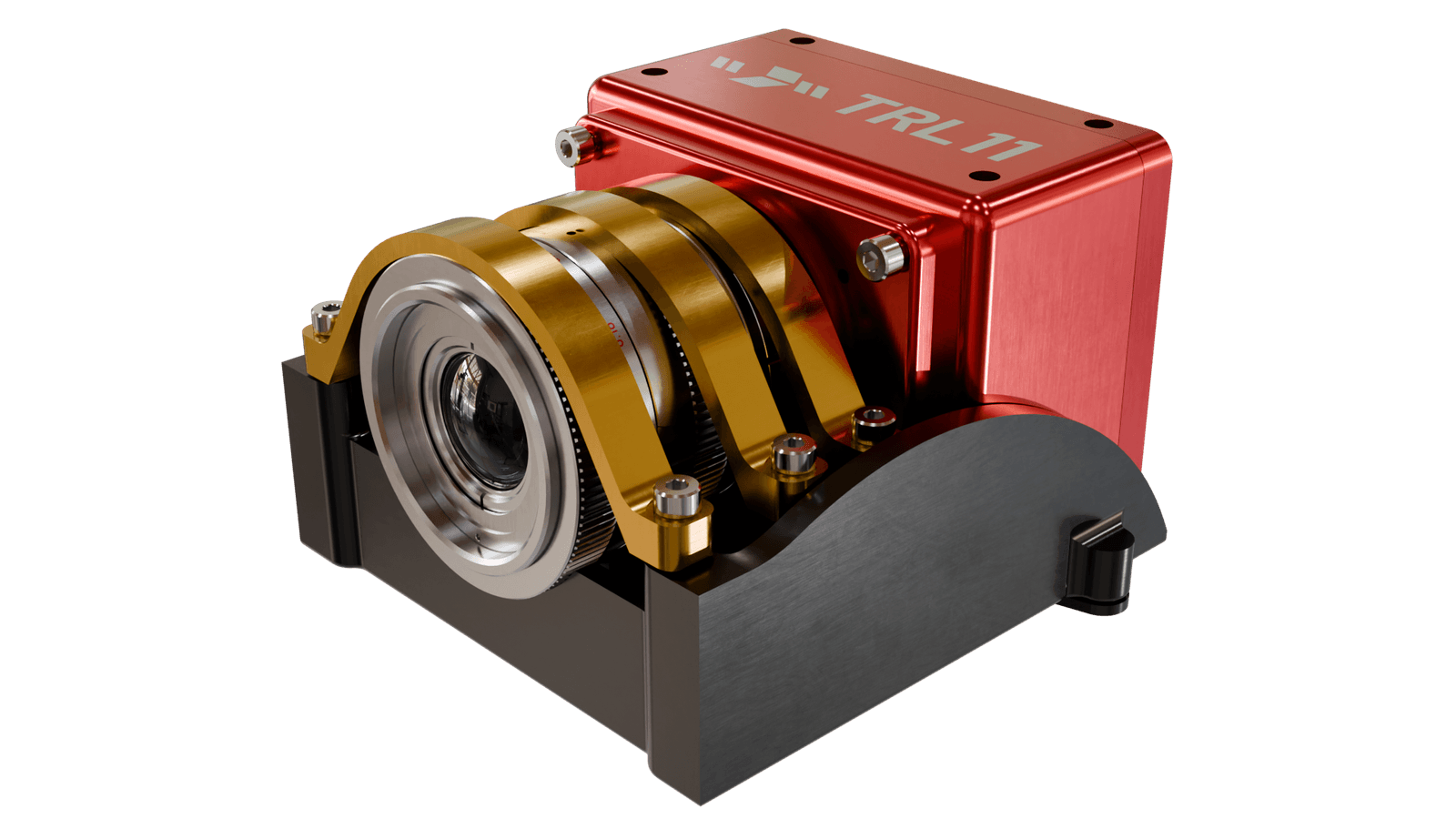
HANS
Along with our DVR and Camera, another device a potential client may need (especially in a system with many cameras) is a space-ready, hardened ethernet switch. This is exactly the purpose that HANS fulfills, and it was the third product that I took the lead of designing within the short period of a couple months.
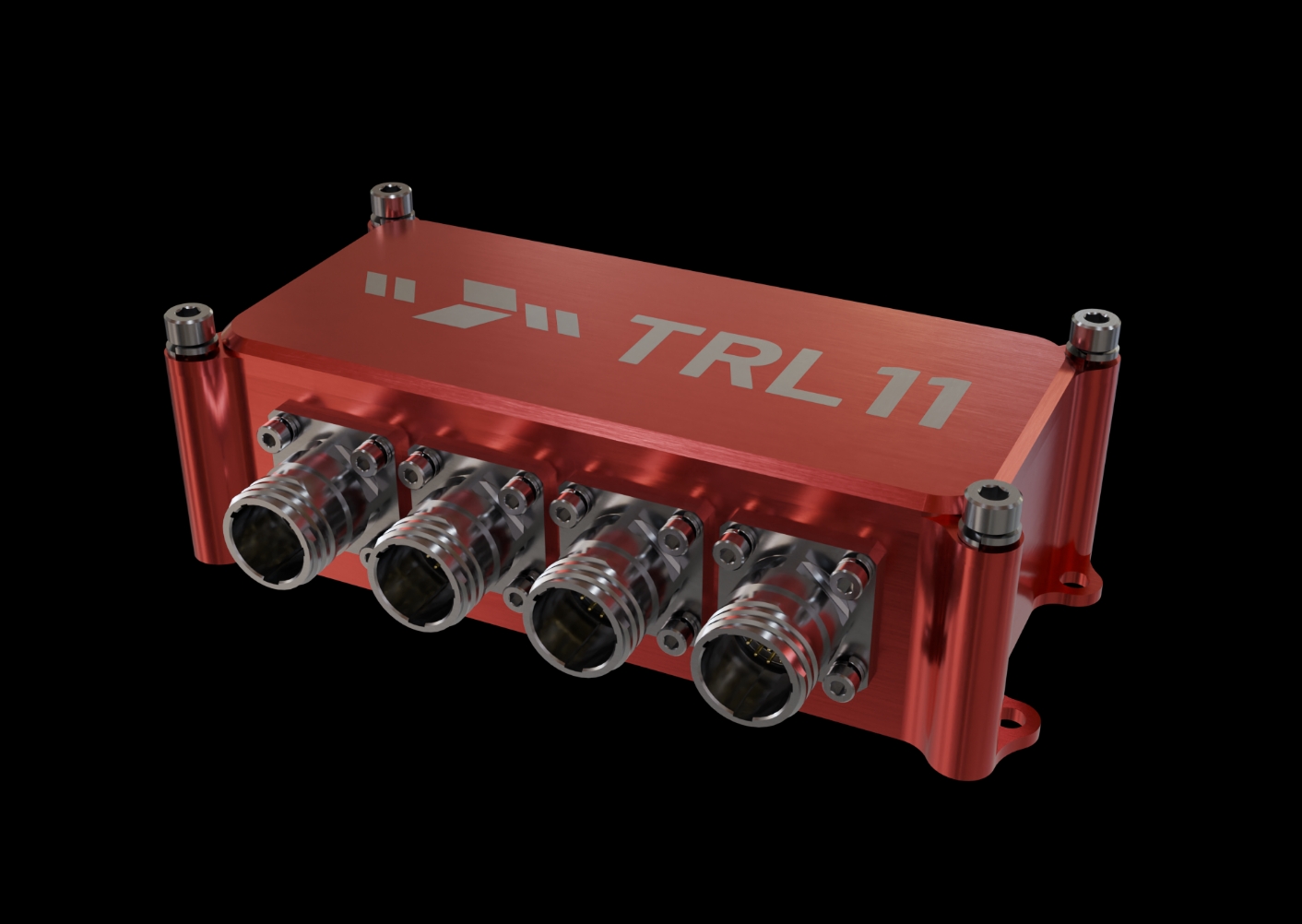
Design Process
The design process of space hardware, especially sensitive optical assemblies, is rigorous. There are countless design requirements and restrictions to consider, and the timeline is always incredibly tight. Here's a condensed list of design considerations I had to keep in mind:
- Size, Weight, Power, and Cost (SWaP-C)
- Design for Manufacturability (DFM)
- Design for Assembly (DFA)
- Electromagnetic Compatibility (EMC)
- Outgassing
- Thermal Performance, especially in a vacuum environment
- Structural Integrity, withstanding applied loads
- Vibrational Modes
- Humidity (in the launch environment)
- Flammability
- Optical Performance
- Static Buildup
- Electrical Harnessing
- Floating Ground
Other Responsibilities
Mechanical design is just the start of the process of developing, testing, launching, and supporting a space-ready video system. In short, additional responsibilities included:
- Writing documentation, including customer-facing ICDs, engineering drawings for manufacturers, and precise assembly instructions for our technicians.
- Writing procedures for, conducting, and evaluating the results of, various types of validation testing. These include thermal vacuum (TVAC), thermal cycling (TC), electromagnetic interference (EMI), vibration, and shock testing.
- As mentioned previously, developing photorealistic renderings of our products for business development and marketing initiatives.
- Creating and maintaining BOMs
- Researching and sourcing specialized hardware, manufacturing processes, and services.
Relevant Skills
- Mechanical Design
- Optical Design
- PCBA Design
- Thermal Optimization
- Design for Manufacturability
- Design for Assembly
- Electrical Harnessing
- 3D Printing
- Rendering
- Stress Analysis
- Thermal Analysis
- Modal Analysis
- Technical Documentation
- Project Management